Easy-Set Multihead Truss Press
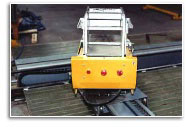
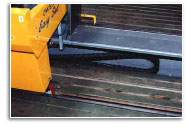
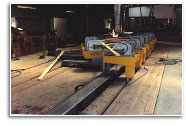
Production Description
The Easy-Set Multi-Head press combines the rapid pressing cycle of multi head presses, with the speed and ease of setup associated with the popular Flo-jig Systems. Flo-jigs have been the main production facility of many truss plants, as they can readily handle a wide variety of truss shapes.
The Easy-Set Multi-Head press has been developed for short production runs and is capable of efficiently manufacturing many of the more complex truss shapes for which conventional multihead presses are not suitable. Generally, multi head presses have not been considered suitable for production runs of 10 trusses or less. However, on the Easy-Set, with quick action air clamps and measuring tapes incorporated in the jig, truss runs of one or two are feasible.
The production cycle time is also improved compared with other multi heads, as the Easy-Set Multi-Head press incorporates nail plate placement. Typically, cycle time for an A Type truss, including placing of timber and unloading finished truss, is 50 seconds. The flow of material to the press and the removal of finished trusses will determine the overall productivity of the machine.
- Length 15400mm
- Width 5135mm
- Height 1120mm
Overall Dimensions
- Fast set-up (3.5 to 4.5 minutes).
- Clear working area.
- Movable operator console with interlocked controls, cat-track tracking on air and hydraulic lines.
- Walk-in design.
- Pneumatic locking of press head positioning along rail.
- Camber adjustment on each press head.
- Pneumatic timber clamps.
- Tooling provided for clamping of truss members.
- 14m heavy duty base rail,
- Four movable arms,
- One fixed apex arm with a 3310mm maximum apex height.
Jig
- Multiple press heads, all joints pressed simultaneously.
- Press heads not required to be used may be isolated and set to one end of the jig.
- Very fast cycle time (40 to 50 seconds).
- Automatic nail plate feeders:
- Interchangeable cartridges to suit different nail plate sizes.
- Adjustable plate pusher to accurately position the nail plate.
- Nail plates picked up and held in position with magnets.
- Anti-tilt press head suspension prevents displacement of connectors and webs during pressing operation.
- Press heads retract following pressing allowing operators to easily lift the finished truss clear of the jig.
- Emergency stop button on each press head.
Press
Specifications
Configuration - C-Frame press heads each mounted on an individual carriage. Carriage is manually orientated and moved along steel rails to the truss panel point. Cartridge on press head for automatic feeding of nail plates. All hoses and cabling under timber floor.
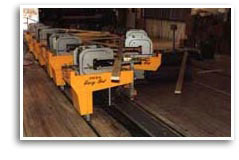
- Maximum span of truss: 14m (or customer specified).
- Maximum height of truss: 3310mm.
- This press is able to press any truss that has all its panel points joining with a chord.
- Any truss with internal plates cannot be pressed.
- Any truss that has plates that require more than 25 Tonne pressing force cannot be pressed.
- Any joint that is closer than 400mm from an adjacent joint cannot be pressed.
- Commonly installed with a Gantry Press, this allows larger plates, internal joints and plates that are close together to be pressed.
Truss Information
- 5 press heads.
- 30 Tonne press heads.
Options
Extra optional automatic nail plate feeders, which have an adjustable magazine with thumb screw adjustment and will fit most size nail plates up to 150 x 150. MiTek does not recommend the use of auto nail feed on very small plates used at T1 points, as the positioning of these points creep, depending on variation in tolerance of timber sizes and accuracy of sawing. Where unusual plate locations are required, the auto nail plate feed can be simply turned off as required, and the nail plates placed manually.
Owen Easyset Multi-Head Jack-Jig
The Easyset Multi-head Jack-jig has been designed specifically for the fast manufacture of hip and jack trusses. This machine incorporates several features which provide an advantage over production of similar trusses using table presses or drop hammers.
A specially designed jig is used incorporating a fixed bottom chord rail and top chord rail that is adjusted in a few seconds to the pitch and span of the truss. This ensures that all trusses in a job are speedily setup up and retain the same shape. Multiple C-frame press heads can be positioned as required anywhere along the jig rails enabling all nail plates at every panel point to be pressed simultaneously. Operators are not required to handle nail plates during the truss setup and pressing processes. Nail plate cartridges and feeding system are used to automatically position nail plates on the press platens in readiness for the next press.
- Fast set-up
- Easily adjustable jig rails,
- Automatic nail plate feeding of press platens,
- Sliding angle & timber rest tooling rests against truss members.
- Fast pressing time - press head at each panel point.
- Very fast cycle time.
- Less floor space required than for table press – jig setup and pressing occur in the same area.
- Retracting press heads for easy truss setup and handling of trusses following pressing.
- Pneumatic locking of press head position on rails.
- Camber adjustment on each press head.
- Pneumatic timber clamps.
- Adjustable cartridges for different nail plate sizes (automatic model only).
- Simple and safe operation
- Push button control panel located away from the pressing area.
- 30mm gap between platens when fully closed.
- Manual mode allowing operator to step through pressing sequence one step at a time.
- Standard configuration - Fixed base rail with three moving pressing stations with 6000mm of travel. Top chord rail pivots about one end of the base rail from 12 up to 35 degrees. Two pressing stations on top chord rail with 5.52m of travel.
- Jig height - 730mm.
- Setup time for truss - 2-3 minutes (operator dependent).
Jig
- Power requirements - 415V AC, 3-phase/neutral, 32A.
- Air requirements - 550kPa, (80psi), 15 l/min.
- Five press heads - 16 Tonne per head.
- Designed to press softwood trusses.
- Press head throat opening (between top and bottom platens) - 90mm open, 30mm closed.
- 10 nail plate cartridges supplied with a standard system. (To suit plate sizes 150x100, 125x75, 100x100, 100x40, or as required by customer).
- Press hydraulic power pack motor - 11kW.
- Maximum operating pressure - 2200kPa, (319psi).
- Pressing cycle time - 20 seconds approximately (operator dependent).
Press
- Maximum span of truss - 6000mm.
- Maximum height of truss - 4200mm.
- Maximum timber width - 200mm (approximately).
- Bottom chord and top chord joints minimum 550mm apart.
- Bottom chord to heel and top chord to heel joints minimum 800mm apart.
- This press is able to press any truss that has all its panel points joining with a chord.
- Any truss with internal plates cannot be pressed.
- Any truss that has plates that require more than the rated pressing force cannot be pressed.
- Safe working area
Truss Information
Options
- Press heads 18 Tonnes.
- Nail plate cartridge variations to suit customer.